Harmonized system simplifies tests of mechanical loads
The optimization of hybrid and electric vehicles does not only extend to the electric drivetrain, but also includes all vehicle components. The aim is to save weight in order to achieve maximum performance and energy efficiency. At the same time, the vehicle must be permanently stable and safely designed for the planned service life. For this reason, chassis components are also tested and continuously improved with regard to mechanical stress. Measurement modules from CSM and telemetry measurement technology from AXON are used to measure the fatigue strength of parts of the wheel suspension.

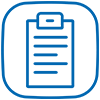
Simulation and validation
The control arms and track rods are part of the unsprung masses and have a significant influence on driving dynamics and ride comfort. The expected forces that occur during various driving situations are predicted in simulations during development and must then be validated in road tests and on the test bench. To validate the simulations, the forces acting on the axle geometry are determined.
Measurement Task
Measurement of forces on control arms and tie rods as well as measurement of spring travel, steering angle and speed.
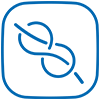
What should be considered?
To measure the durability the acting forces as well as the suspension travel, steering angle and speed must be measured. For a simple application, all measured variables are recorded in parallel with one measurement system. Data is collected during different driving situations as well as on the test bench. The measurement system used should be able to be used in all test scenarios in order to avoid long conversion times and to enable simple comparison of the data obtained.
Component-specific requirements
Tie rods and control arms are very stable components, which means that only low strain values are to be expected in normal driving situations. The measurement technology used must therefore be very high-resolution in order to record very small signal values. However, since very high values can occur during misuse tests, such as driving over a curb, the measurement technology must offer sufficient dynamics. In addition, when measuring rotating parts, there are difficulties in transmitting the values as the sensors have to be attached to the shaft.

Combine all data in one measurement system
Components from the Vector CSM E-Mobility Measurement System are used for the measurements. The tensile/compression load in the tie rods is measured using strain gauges. Depending on the geometric design of the axle control arm, strain gauges are used to measure individual strains, bending or tensile/compressive loads.
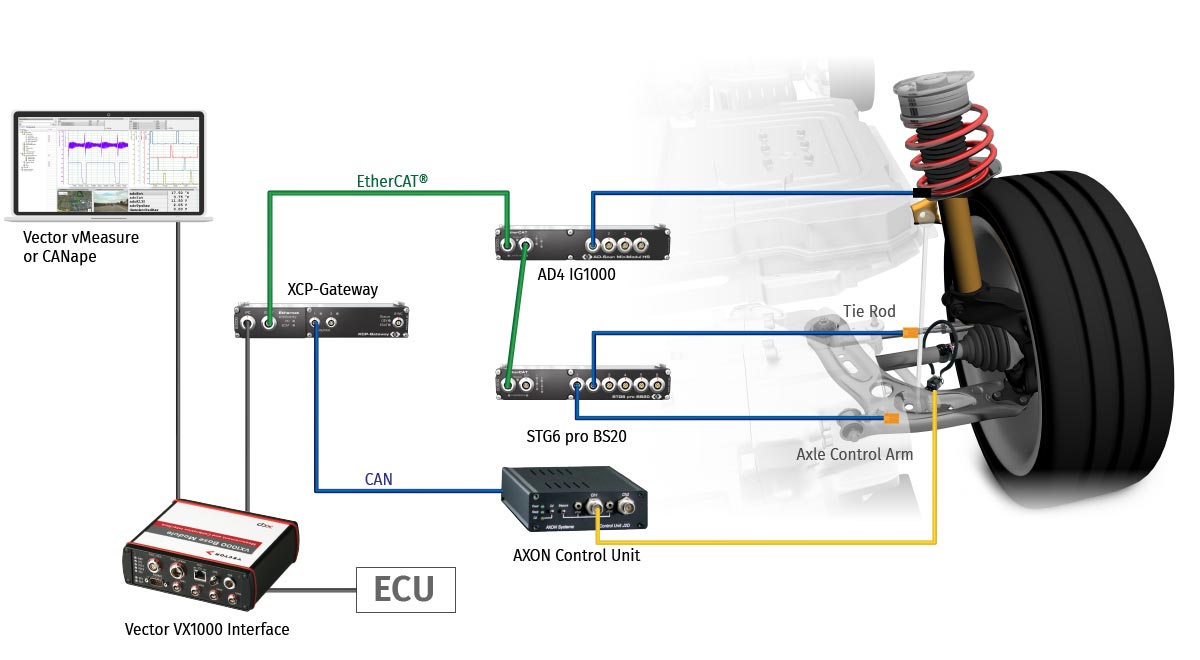
Automatically adjusted in the measurement module
All strain gauges are connected to a STG6 pro BS20 strain gage measurement module. Quarter bridges are added directly in the sensor cable to form half bridges. The strain gauge is simply added to the full bridge in the measurement module, eliminating the need for further wiring and allowing a wide range of strain gauge resistance values to be supported. Thanks to the extremely low input voltage range of up to ±0.3 mV/V, very small measurement signals can be precisely recorded. The measurement data rate of up to 20 kHz per channel allows the detection of rapid load changes.
Measurements on rotating parts
Telemetry systems for recording torques from AXON Systems GmbH, a long-standing partner of CSM, are used for the measurements on the drive shaft. With the solution from AXON, the data from a rotating strain gauge measurement point for torque measurement are transmitted without contact. For this purpose, the strain gauge measurement point is connected to a rotor electronics unit, which is installed on the drive shaft and provided with a multi-layer protective coating so that environmental influences do not affect the measurement results. The data is transmitted wirelessly to a stator unit, the antenna of which is placed in a ring around the axle. The antenna of the stator unit can be freely shaped and thus flexibly adapted to the conditions at the installation site with little installation space. The control unit generates the necessary supply voltage for the sensors on the rotor unit and forwards the recorded measurement data.
Simply merge signals for analysis
The CSM measurement modules are connected to an XCP-Gateway via EtherCAT®. The XCP-Gateway synchronizes the measurement modules via the Precision Time Protocol (PTP) better than 1 μs and converts all signals to XCP-on-Ethernet. The data from the AXON telemetry system is integrated into the measurement chain via CAN, bundled in the XCP-Gateway and also forwarded via XCP-on-Ethernet. The collected data can be recorded either with a data logger or a measurement computer. The subsequent data evaluation can be carried out with Vector CANape or vMeasure.



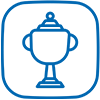
Suitable measurement technology for high requirements
With the components of the Vector CSM E-Mobility Measurement System and measurement technology from AXON, all required measurement variables can be acquired precisely with a standardized system. Thanks to the compact and robust design, the measurement modules and telemetry systems can be installed close to the measurement point and used both in road tests and on the test bench.

More information
Related Products
Related Hardware
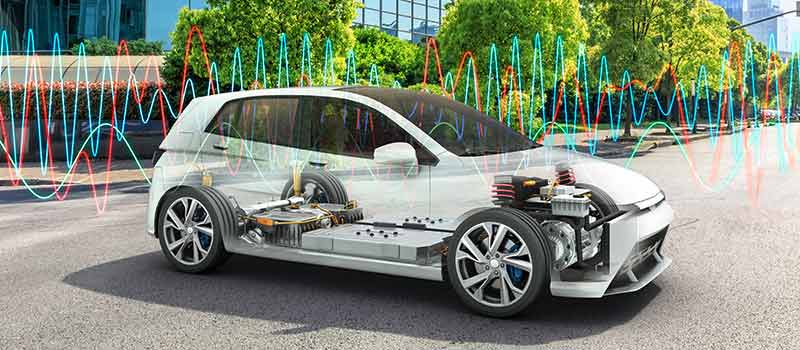
The Vector CSM E-Mobility Measurement System
The measurement system for the development of electric mobility

STG6 ECAT MM-Series
Fast distributed strain gauge measurements
Type STG6 pro BS20 | STG6 BK20
EtherCAT®-based measurement modules for decentralized use under demanding conditions: Robust, very compact and with six time-synchronous strain gauge inputs for quarter, half and full bridges.

XCP-Gateway
The protocol converter for EtherCAT® and CAN to XCP-on-Ethernet
XCP-Gateway is the interface between the data acquisition software (e. g. vMeasure, CANape®, INCA®, Vision® ...) and the EtherCAT® measurement modules from CSM. It includes an EtherCAT® master and an XCP-on-Ethernet slave.
Related Software
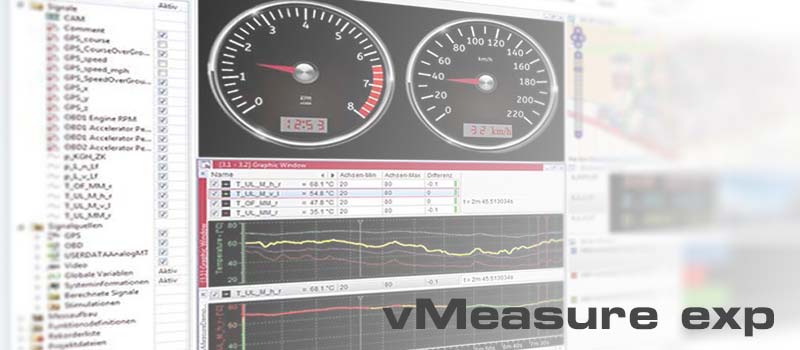
vMeasure
Reliably Solving Complex Measurement Tasks
vMeasure is a subset of CANape focused on measurement. It is an easy-to-use software tool for the acquisition and analysis of measurement data that can be used in combination with all CAN- and EtherCAT®-based CSM measurement modules. CSMconfig was integrated directly to ensure swift configuration.

Swift configuration of measurement chains: CSMconfig is the reliable configuration software for all CAN and EtherCAT® based measurement modules from CSM. The clearly arranged and easy-to-use user interface allows an easy setting of all measurement parameters. This helps speeding up the measurement setup considerably.